Glob tops and dam-fill encapsulants are epoxies used to seal chips in chip-on-board applications. Their design provides both environmental protection (meeting the latest Europe green requirements) as well as enhancement of mechanical robustness for fragile semiconductor devices, components, and wire bond packages.
These materials are highly filled with silica filler for low coefficient of thermal expansion or CTE. The CTE measures how much the material expands at different temperatures. We utilize high purity epoxy resins to protect sensitive electrical components since some epoxies will emit chemicals such as chlorine gas, which affects performance.
Our encapsulants can be applied in two different ways to protect sensitive components. These methods are the Dam-and-Fill Process and glob top Process. Let’s discuss each in more detail next.
Dam and Fill Process for Encapsulants
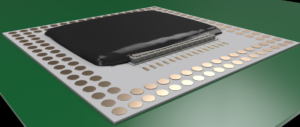
An encapsulant manufactured via the Dam and Fill Process. The encapsulant creates a protective barrier around the high-tech components.
First, we dispense a viscous material to create a dam around the perimeter of components. We formulate this material to have a high aspect ratio after dispensing in order to provide a protective barrier. After the wall is completed around the parts, a second material, called the fill, is dispensed with good flow to fill the cavity. This material has self-leveling characteristics so that it can create a smooth, flat top so that it can fit inside the electronic device without adding bulk.
Glob Top Process for Encapsulants
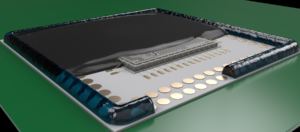
In glob top encapsulation, sealant is applied directly to the sensitive electronics to protect crucial components and devices.
The glob top process is slightly different. In this process, encapsulant material is dispensed directly to an area to protect critical components and devices. The glob top material is first dispensed onto the component using a needle. The material will flow to cover the component. There is a need to control rheology (material flow properties) so that the material flows enough to cover the component but doesn’t spread to adjacent parts.
What Glob Tops and Dam-Fill Encapsulants?
Our encapsulants and sealants provide features and benefits including:
• Outstanding adhesion to a wide variety of substrates
• High glass transition temperature or Tg – which means better encapsulation and protection
• Low CTE for use near highly sensitive electronic devices and high-tech components
• High modulus (stiffness) for strength and robustness
• Design for high reliability and harsh environments (mainly automotive and industrial applications, but also medical uses such as pacemakers)
• Excellent insulation (high bias voltage) to protect critical components
• Designed for high volume production, capable of jet or syringe dispensing, with long pot life and fast curing time.
• Compliance with the European Union’s REACH and RoHS requirements for not containing hazardous materials
NAMICS outshines the competitors through excellent, efficient customer service. Our lead times are shorter than those of our competitors. NAMICS products are designed to meet upcoming European environmental requirements which begin in 2023.
To learn more about NAMICS, stretchable inks, and how we can become your innovation partner, reach out today.